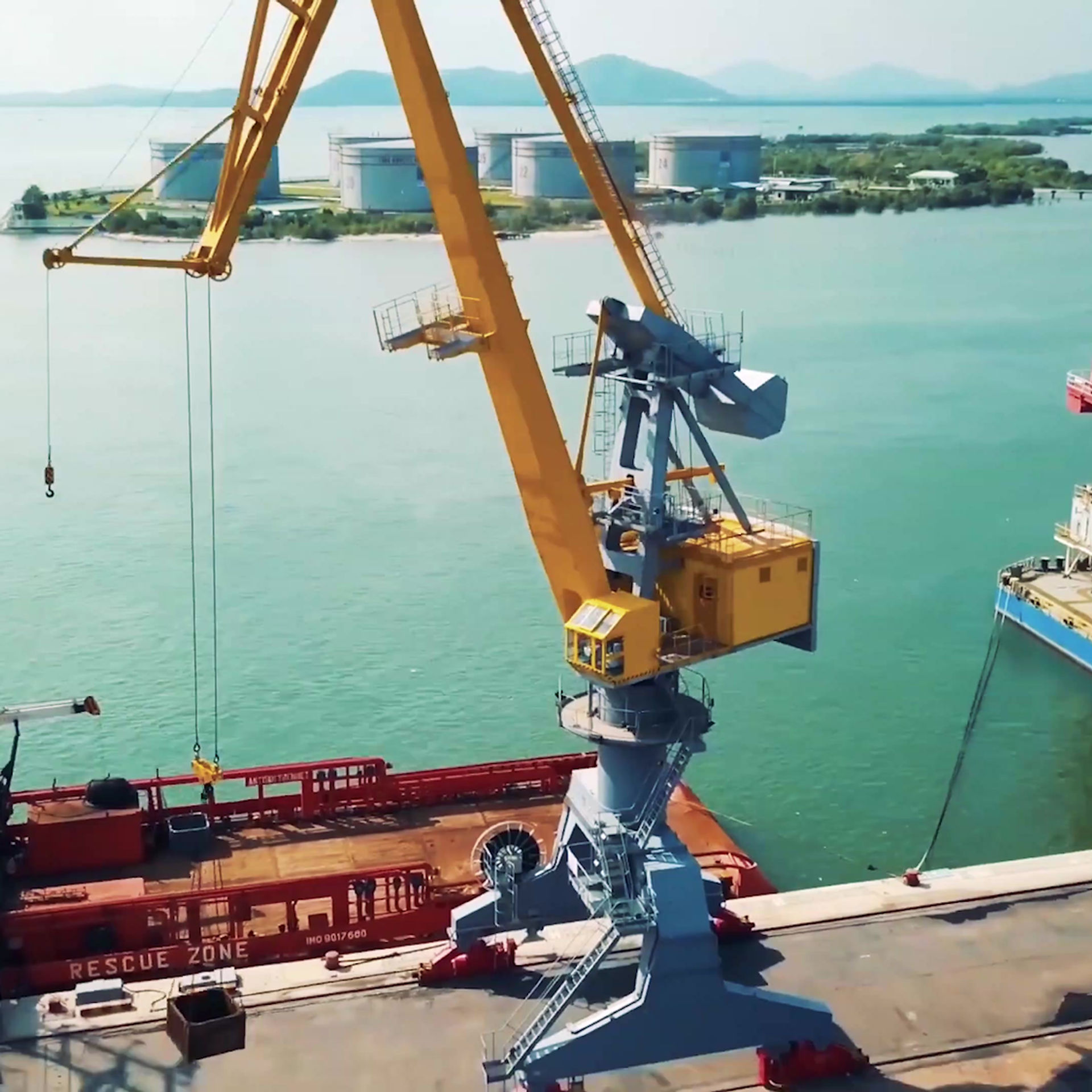
Ngôn ngữ
Các tính năng của máy dỡ hàng liên tục kiểu vít
Efficient: The ship unloading quota efficiency ranges from 100T/H to 2700T/H, meeting the needs of bulk cargo operations along the river and the coast. Due to the use of a special structure of the forced feeding device and high-speed spiral, the material is quickly lifted, thus the unloading capacity is large, and the actual unloading capacity is greater than the rated unloading capacity.
Strong adaptability: strong adaptability to cargo and ship type. The spiral ship unloader can be used to unload various powder, granular and block materials. When unloading some materials that are compacted or even form a hard shell after sea transportation, such as fertilizer, cement, potassium salt, etc., due to the reverse feeding spiral or loosening cutter installed outside the feeding device, it has the function of making the material loose and can meet the ship unloading requirements well. The vertical part of the spiral ship unloader has a small cross-sectional size, and the auxiliary mechanisms such as walking, rotation, pitching, and swinging ensure the flexible movement of the machine, and it can be suitable for various types of barges and sea ships.
Energy consumption: high energy consumption. Due to the friction between the material and the spiral surface, the friction between the material and the trough or the conveying pipe wall, and the friction and stirring between the materials, the unit length movement resistance of the material is large, which makes the unit energy consumption of the spiral ship unloader higher than other mechanical continuous ship unloaders, and comparable to the grab ship unloader, but much lower than the pneumatic ship unloader. The average power consumption is 20~28% of the same pneumatic ship unloader. For unloading materials with small specific gravity, good fluidity, and small abrasiveness, such as cement, grain, coal, etc., the unit energy consumption is low, while for unloading materials with large specific gravity and abrasiveness, such as phosphate, iron ore powder, etc., the unit energy consumption will increase significantly. Due to the light transmission parts, it can work continuously; it can also use the whole machine frequency conversion treatment, which can save electricity consumption. Its power consumption varies with the type of cargo and the rated unloading capacity. For every ton of cement unloaded, the power consumption is 0.50- -0. 79 kWh. The energy saving effect is remarkable. And the clearing machine is used less, and its fuel consumption is about 30% of the grab ship unloader. Now small wheel rakes are widely used, and some are electrically driven.
Environmental protection: The material conveying system of the spiral ship unloader is fully enclosed, and all connection points are of closed design, which prevents the overflow of dust and material; there is no dust flying or material or material odor leakage during the ship unloading process. The feeder is buried in the material, thus reducing the amount of dust generated by the feeding. For unloading materials that easily pollute the air, such as cement, coal dust, chalk powder, potassium salt, ammonium phosphate, etc., using a spiral ship unloader is especially beneficial. The noise of the spiral ship unloader is also small. The main components are tested and corrected by static balance and dynamic balance. The equipment runs smoothly and reliably, and will not cause noise pollution to the surrounding environment. The sound level can be controlled below 60dB(A).
Simple structure: The spiral ship unloader is light in weight and simple in structure. The material conveying system of the spiral ship unloader is composed of a spiral conveyor with no flexible traction components, and the conveyor has no return branch, which is relatively simple in structure, and the cross-sectional size of the vertical arm and the horizontal arm is small. Under the same conditions of productivity and object ship, the weight of the spiral ship unloader is much smaller than that of the grab ship unloader, and it is also the smallest one among various mechanical continuous ship unloaders. Therefore, the cost of the spiral ship unloader is low, and the requirements for the bearing capacity of the terminal are low.
Reduce costs: The energy saving and work reliability greatly reduce the long-term operation cost of the ship unloader. Reduce labor, only one person is required to operate, observe the material situation in the cabin on one side, and operate the portable remote control on the other. Save voyage fees, the continuous andefficient unloading performance of the ship unloader greatly shortens the unloading time, and can save tens of thousands or even tens of thousands of voyage fees a day.
Full-featured: The overall mechatronics design, all controls are controlled by imported PLC programmable controllers, the program can be easily modified, the degree of automation is high, and it also has various safety protection functions such as mechanical protection, hydraulic automatic protection, speed limit protection, overload protection, electromagnetic and frequency conversion combined braking system.
The wear of the working components is more serious. The main wear-prone parts of the spiral ship unloader are the conveying spiral and the intermediate support bearing of the vertical spiral conveyor. Since the relative sliding of the spiral and the material, and the relative sliding between the edge of the intermediate bearing and the bushing are unavoidable, the main method to improve the service life of the working components is to use materials with good wear resistance, which will increase the cost of the spiral ship unloader.
Technical characteristics of spiral ship unloader: Widely used in building materials transfer terminals, power, chemical, food and other industries, suitable for horizontal, vertical or any angle, conveying powdery, granular and small block materials, such as cement, coal ash, ore powder, fertilizer, grain, etc.; its working environment temperature is -20-+40℃, the conveying material temperature is -20-+80℃, and it is not suitable for conveying materials with high viscosity.